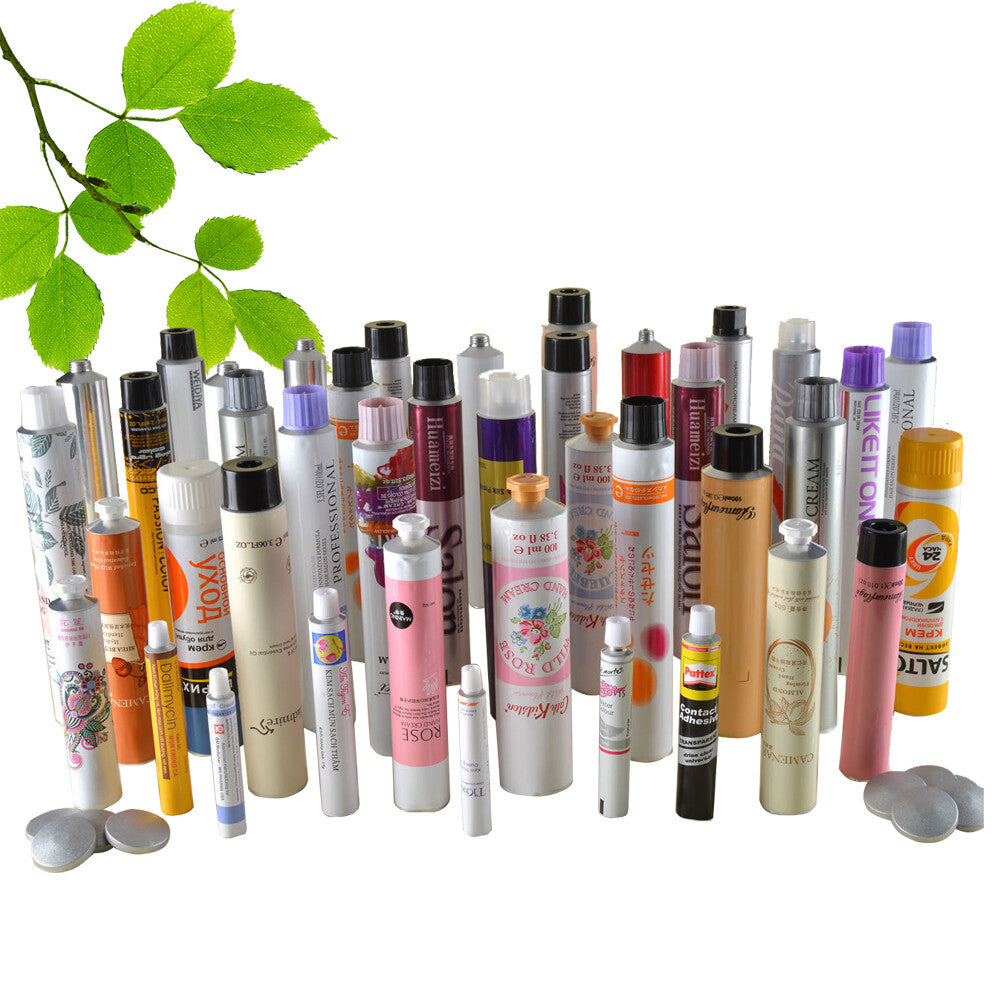
Aluminum Tubes | For Cosmetic Skincare Ingredients.
Aluminum Tube | Bulk Sales
any size and fill capacity, full range of printing.
Our tubes are 100% food grade aluminum FDA and EU approved.
Select any style cap that goes with your design.
Sample Lead time:
10 days,
Production lead:
after sample is approved, production lead time for Tube is 10 days, w/ full color print 20 days.
Free Shipping,
Door to door shipping, tax, import docs are included.
See sustainable certification here.
What is Aluminum?
Aluminum (Aluminium) – a silver-white, soft metal, noted for lightness, high reflectivity, high thermal conductivity, high electrical conductivity, nontoxicity, and corrosion resistance. Aluminum is the most abundant metallic element, comprising 1/12th of the earth’s crust. However, it is never found in nature as an elemental metal but only combined with oxygen and other elements. In ordinary language, aluminum often means aluminum alloy.
Among all kind of metal materials, aluminum wins out either because its properties and performance are superior or because fabrication techniques enable the finished product to be manufactured at a competitive cost. The usage of aluminum continues to increase and expand; new markets such as the automotive sector are beginning to recognize its true unparalleled benefits.
Where and how to get aluminum?
Bauxite, a mineral mined from the earth is the major source of aluminum. The bauxite is crushed and sprayed with water, clay and silica removed, and then kiln-dried, and mixed with soda ash and crushed lime. The mixture is then processed in a digester, then reduced under pressure and sent to a settling tank where additional impurities are removed.
After filtering, cooling, and further processing in a precipitator, the mixture is thickened and filtered once more before being heated in a calcinating kiln. The resultant material is alumina, a powdery chemical combination of oxygen and aluminum.
Smelting
Alumina has to go through smelting and alloying processes to become aluminum of common use. An aluminum smelter contains a cryolite bath (in which the mineral cryolite is melted using electrical current). Alumina, in powder form, is placed into the cryolite bath, where it is melted and separated from its oxygen component, settling beneath the cryolite. The molten aluminum is siphoned from the bottom of the smelter and placed in a crucible, then formed into ingot or transferred to an alloying furnace.
Alloying
In the alloying furnace, the aluminum ingot is melted, and mixed with alloying metals like Magnesium, silica, copper, etc to form a aluminum alloy which offer a wide range of specific material properties. The physical properties of the alloy are very much determined by the alloy content.
For example:
- Zinc tends to offer very high strength
- Manganese offers good corrosion resistance
- Copper yields excellent machinability
- Magnesium is good for welding applications
The molten metal mixture is then cast into solid logs. Logs may be cut to obtain a more manageable billet. Logs and billets are sent to extruders for aluminum extrusion.
Key Characteristics of aluminum
Aluminum when used in sheet, coil or extruded form has a number of advantages over other metals and materials. Where as other materials may offer some of the beneficial characteristics of aluminum, they cannot provide the full range of benefits that aluminum can. Aluminum extruding is a versatile metal-forming process that enables designers, engineers, and manufacturers to take full advantage of a wide array of physical characteristics:
Light Weight
Aluminum has specific gravity of 2.7 and weighs only 0.1 pound per cubic inch. It weighs less by volume than most other metals. In fact, it is about one-third the weight of iron, steel, copper, or brass. Lightweight aluminum is easier to handle, less expensive to ship, and is an attractive material for applications in fields such as aerospace, high-rise construction, and automotive design. When used in the transportation field it can yield significant benefits in a reduction of fuel usage.
Strong
Aluminum profiles can be made as strong as needed for most applications. When temperature falls, it becomes even stronger, so it is most commonly used material in cold area
High Strength-to-Weight Ratio
Aluminum offers an incredible combination of lightweight and high strength. Higher strengths can be obtained by adding one or more of the following: manganese, silicon, copper, magnesium, or zinc. Increases can also be accomplished by specialized heat treatments. Nowadays, the aerospace industry and the automotive industry heavily depend on aluminum as the material.
Corrosion resistance
The excellent corrosion resistance of aluminum is due to the presence of a thin, hard protective film of aluminum oxide that bonds tenaciously to the surface. This occurs naturally and can reach a thickness of 0.2 millionths of an inch. Further protection can be done by applying paint or an anodize finish. Unlike steel aluminum will not rust.